29th Apr 2024
Sioux Pneumatic Screwdrivers | Precision Tools for Production Fastening
A pneumatic screwdriver is a powerful, air-powered tool that allows for the production fastening of screws in an assembly plant environment. Commonly used by furniture manufacturers, sheet metal fabricators, aerospace plants, and automotive assembly lines, these versatile tools increase assembly speed and ensure a proper torqued fastener. Keep reading to understand the mechanics and applications behind pneumatic screwdrivers, focusing particularly on Sioux Pneumatic Screwdrivers, renowned for their reliability and performance. Not only are Sioux air tools workhorses in general but they are also proudly made in Murphy, North Carolina, USA.
How a Pneumatic Screwdriver Works
A pneumatic screwdriver operates by harnessing compressed air to rotate screws. Through a connected air hose, the tool receives compressed air which powers its motor, subsequently driving the screwdriver bit. Activation of the trigger initiates the flow of compressed air into the engine via a valve, enabling the turning of the bit to fasten screws into various materials. The pressure level of the air supply or a mechanical, spring-adjustable clutch modulates the torque the tool produces.
Components of a Pneumatic Screwdriver
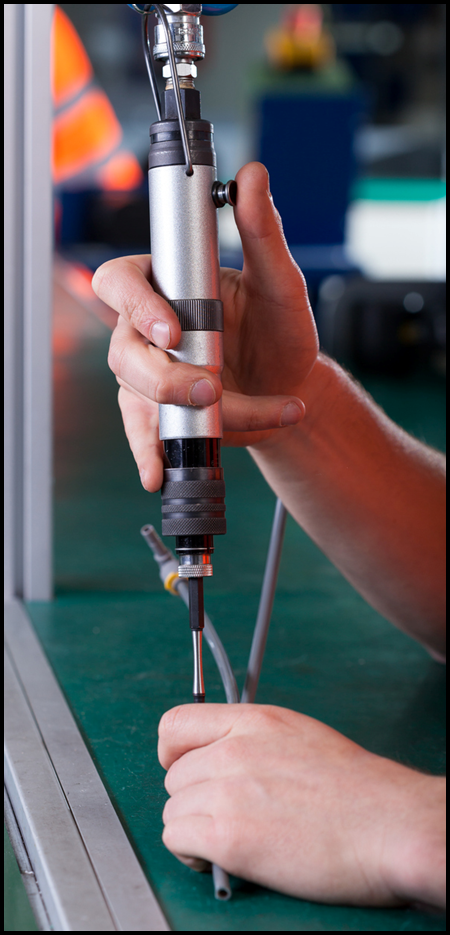
- Throttle Valve: This component, which is located at the heart of a pneumatic tool, helps with regulating the flow of compressed air.
- Motor: Compressed air, directed over phenolic vanes, drives rotation, generating horsepower and powering the screwdriver.
- Clutch: This feature is essential for controlling torque, ensuring precise fastening by disengaging when the desired torque is reached.
- Gearing: A gear reduction system fine-tunes the output to the required RPM range and torque level for optimized performance.
- Trigger: Operators activate the screwdriver via the trigger, enabling precise control over fastening operations (note: some models of tools use push-to-start activation instead of a trigger mechanism)
- Comfort Grip: Ergonomically designed handles increase comfort during prolonged use, reducing operator fatigue.
- Quick Change Chuck: This is the screwdriver bit holder that facilitates swift fastener tool changes for a seamless transition between tasks.
- Clutch Housing: This component houses the clutch mechanism for its protection and access when torque changes are required during calibration.
Pneumatic screwdrivers stand out from the crowd for several reasons. Their superior power tackles tough materials with ease, making them ideal for jobs that would leave manual or electric screwdrivers struggling. Their speed machines allow users to zip through projects in record time for fast project completion. Also, their lightweight design makes them comfortable to use for extended periods, effectively reducing fatigue. Pneumatic screwdrivers boast impressive durability capable of withstanding heavy-duty usage without compromising performance.
Types of Pneumatic Screwdriver Clutches
Pneumatic screwdriver clutches are mechanisms that regulate the amount of torque applied to a fastener when driving screws. These clutches are crucial for preventing over-tightening or stripping screws, thus improving quality and reducing defects. Controlling the torque output helps maintain the integrity of work materials and minimize the risk of damage during the assembly process.
By either adjusting air pressure or tightening or loosening the torque spring, users can tailor torque levels according to the specific application requirements. Four basic types of pneumatic screwdriver clutches are available: direct drive, positive, adjustable, and torque control:
Drill Handling Safety Tips
Direct Drive:
Direct Drive Clutches are the workhorses of the bunch. These simple and economical designs offer no frills – they simply transfer power from the motor straight to the output spindle. However, the lack of automatic shut-off requires constant operator attention to avoid over-tightening and damaging screws or materials. These are best used in the hands of well-trained operators, where precise torque control is not required.
Positive Clutches:
Positive Clutches prioritize safety and consistency. They only engage when the operator applies forward pressure to the bit of the tool and automatically disengage when the torque of the fastener overcomes the power produced by the motor, thus causing the clutch jaws to disengage and bit rotation to halt. If they desire additional torque, the operator can push forward to re-engage the clutch jaws to try to milk the tool for a few additional inch lbs. of torque. Positive clutch tools are good for limited torque control required such as in a furniture assembly plant or for fastening sheet metal screws
Adjustable Clutches:
Also known as Cushion or Ratcheting Clutch, it offers operator control over torque. The calibration laboratory or maintenance personnel can fine-tune the clutch by adjusting a spring-loaded mechanism to deliver specific levels of torque. The tool produces an audible “ratcheting sound” which indicates when it reaches the pre-set torque. A great “all round” clutch well suited to general-purpose assembly applications where a fair amount of torque control is desired.
Torque Control Clutches:
Torque Control Clutches produce the most tight tolerance fastening results with some models reaching repeatability within +/- 10%. Torque-controlled clutches, also known as “shut-off clutches” are sophisticated systems that utilize a two-cam setup to regulate air supply to the motor with precision. When it reaches the desired torque setting, the clutch “cams out”, shutting off airflow to the tool which in turn stops rotation. An excellent clutch when fastening critical joints and precision torque control is mandatory. You can find these clutches in electronics and lighting assembly facilities as well as in aerospace and automotive plants.
The Awesome Serviceability of Sioux Pneumatic Screwdrivers
Like anything, precision fastening screwdrivers require maintenance from time to time. The goal is to return the tool to the production line with as little downtime as possible. Serviceability is paramount in reducing operating costs and ensuring peak performance. Sioux Pneumatic Screwdrivers offer ease of maintenance. Key features contributing to their serviceability include:
Accessible Tipper Valve and Valve Seat
Typically located by the air inlet, these two components work together to control the flow of compressed air to the tool. The valve regulates the air entering the motor, while the valve seat provides a tight seal to ensure efficient operation and prevent leaks. Unlike some screwdrivers where these components require intricate disassembly, Sioux offers readily accessible tipper valves and valve seats. It allows for swift inspection, cleaning, or replacement during routine maintenance, minimizing downtime and ensuring optimum tool performance.
Drop-In Motors
Replacing a worn motor can be a time-consuming process on some tools. Sioux simplifies this with a drop-in motor, which is a pre-assembled unit for effortless motor replacements. It eliminates complex disassembly and speeds up repairs. You can swap pre-assembled units quickly without complicated and time-consuming disassembly work, saving valuable time and getting you back to work faster. Keep pre-assembled, backup motors on the shelf ready to go. When a screwdriver starts losing power on the line, you can install a replacement motor within minutes not hours. Spent motors requiring rebuilding can be sent to qualified maintenance personnel or returned to an authorized Sioux tool repair facility.
Case-Hardened Rotor Pinion
The rotor pinion is a critical component that transmits power within the screwdriver by meshing with gears, like a mini crankshaft. Sioux uses a case-hardened rotor pinion. This special treatment boosts its durability, reducing the likelihood of wear and tear that could necessitate premature maintenance. By extending the pinion's lifespan, Sioux minimizes the need for frequent service and keeps your screwdriver running longer.
Convenient Lubrication via Grease Zerk Fitting
Regular lubrication is essential for maintaining peak performance and extending the life of any tool. On a Sioux screwdriver, a grease Zerk fitting (a fitting that resembles a small nipple) provides a convenient lubrication point where maintenance personnel can inject grease into the tool without disassembly; this allows for quick, mess-free greasing of the tool gear chain. Note: do not inject grease into the air inlet of any air tool.
Integrated Ring Gear and Slip-Fit Planetary Gear Pins and Front Endplate Bearing
Sioux incorporates innovative design elements that simplify disassembly and reassembly. The ring gear is a toothed wheel that meshes with the pinion gear to transmit rotational force. The slip-fit planetary gear pins allow easy removal and installation of the planetary gears during maintenance.
Pins hold the gears in place without requiring complex tools or tight tolerances. The front endplate bearing is at the front of the screwdriver housing to support the rotating shaft and minimize friction. An integrated ring gear eliminates the need for complex alignment procedures during service. The slip-fit design of the planetary gear pins and front endplate bearing allows for effortless removal and installation, further reducing maintenance complexity.
A Side Note on Pneumatic Screwdriver Safety
Even though pneumatic screwdrivers enhance productivity, safety precautions are imperative:

- Eye Protection: Given the potential for airborne debris, proper eye protection is necessary for operators and bystanders. Depending on the specific task, you may also need to wear gloves, ear protection, and dust masks to act as a barrier against flying debris, noise, and other hazards.
- Tool Maintenance: Ensure all parts of the pneumatic screwdriver are in good condition and replace any worn or damaged components for optimum screwdriver performance. Only use suitable bits and adaptors as incompatible bits can damage the screw head or cause the fastener to become lodged or break. Mismatched adaptors can also introduce wobble or slippage, thus increasing the risk of injury and minimizing overall efficiency. Stick to production-grade, hardened bits, and adaptors to protect both the operator and the work.
- Proper Shutdown: Before maintenance or adjustments, deactivate the air supply at the source, typically by turning an in-line valve. This cuts off the flow of compressed air to the tool. Next, release any residual pressure by holding the tool trigger down in a safe direction until all air has been expelled. Finally, disconnect the tool from the air hose to mitigate accidental re-pressurization during your work.
- Maintain Secure Footing: Pneumatic screwdrivers can pack a powerful punch. Sudden and unexpected movements can occur, potentially causing injury. Controlling the tool requires a well-balanced stance with a safe footing. The use of industrial matting is recommended. This enables the user to react to any unexpected movements and helps prevent slips or falls.
Choosing the Best Pneumatic Screwdriver and Clutch for Your Assembly Application
Selecting the right pneumatic screwdriver and clutch type depends on the orientation of the work (vertical versus horizontal) fastener torque requirements, fastener type, and materials to be assembled. For optimal torque control on each job, consider the screwdriver’s torque range, RPM, and clutch type.
Free-Speed RPM is the unloaded rotation speed of the motor. Higher RPMs equate to faster driving speeds and are ideal for the high-volume assembly of fasteners not likely to strip. Lower RPMs offer more control for delicate applications and smaller screws.
For lighter applications like electronics assembly, a low torque, low RPM screwdriver is the call. Operators sometimes prefer the control afforded by a lever start tool in these applications to prevent cross-threading. The throttle can be “feathered” allowing for slower rotation while the fastener is in the initial stages of the rundown.
Higher torque tools are good for driving long wood screws, assembling medium diameter (roughly 1/4” to 7/16”) joints composed of nuts and bolts, or cutting threads when driving sheet metal screws. Always select a tool that has a torque range allowing for a 20% cushion at either end of the range. For example, if your target torque is 30-inch lbs., a screwdriver with a 10-inch lbs. to 40-inch lbs. torque range would be a good choice. You never want to operate a screwdriver right at or near its upper or lower limits. Doing so will decrease the repeatability of the torque applied to the fasteners. Use the 80/20 rule to set the torque in the sweet spot of the tool’s torque range. Overtightening or over-loosening a screwdriver clutch spring will result in poor results.
As discussed above, the clutch plays a pivotal role in controlling the tightening force applied to the screw. Direct, positive, adjustable, and torque-control clutches cater to specific fastening needs. Consider the materials and type of joint to be fastened (hard or soft materials) and select a clutch accordingly.
About Us
International Air Tool and Industrial Supply Co. is your expert source for industrial-grade pneumatic screwdrivers. We are an authorized distributor of Sioux Tools headquartered in San Diego, California USA.
Customer satisfaction is our top priority. We ensure that every purchase meets your expectations. If for any reason you're not completely satisfied with your purchase, we offer a hassle-free return and exchange policy. Our dedicated team is here to assist you before, during, and after the purchase process so that you receive the support, you need to make your experience with us a positive one.
For help choosing the best Sioux Pneumatic Screwdriver for your fastening application, call (800) 608-5210 or email info@intlairtool.com