7th Feb 2024
Efficient Weld Heat Tint Removal: Walter Surfox Electrochemical Cleaning System for Stainless Steel & Aluminum
Walter SURFOX electrochemical weld cleaning system stands out as a remarkably efficient approach for eliminating heat tint from welded stainless steel, including TIG, spot, and pulsed MIG welding, all while preserving the integrity of the parent material's surface. This innovative system encourages the development of a consistent and robust chromium oxide passive layer, providing durable protection against further corrosion.
SURFOX proves to be a superior choice in terms of safety, speed, and cost-effectiveness when compared to the use of highly hazardous pickling pastes and other weld cleaning methods. Its advantages include being SAFE, FAST, and EASY TO USE.
The cleaning electrolytes used in SURFOX are NSF registered, making them suitable for application in food plants, and they present no health hazards for operators. Achieving uniform cleaning and passivation at a rate of 3 to 5 feet per minute, SURFOX ensures efficient results.
Additionally, the integrated reservoir and dispensing pump within the SURFOX system automatically deliver the cleaning electrolyte to the machine's tip, guaranteeing a seamless and uninterrupted cleaning process.
The Importance of Passivation in Preserving Stainless Steel Integrity
Understanding the significance of passivation is crucial for maintaining the corrosion resistance of stainless steel. Stainless steel's ability to withstand corrosion is attributed to the formation of a passive chromium oxide layer on its surface, a process known as passivation. This protective layer is vital for preventing corrosion, and any damage to it, whether through abrasion or excessive heat from welding, exposes the metal to the risk of corrosion.
Initiation and Conditions of Passivation
Passivation initiates when the chromium in stainless steel reacts with oxygen in the air. This chemical reaction results in the formation of a passive chromium oxide layer, offering protection to the stainless steel surface. To ensure the creation of a thick and uniform chromium oxide passive layer, the parent material's surface must be impeccably clean and free from contaminants.
Various factors, such as mechanical abrasion, thermal treatment, welding, exposure to salt, strong acids, and galvanic contamination, can compromise the chromium oxide layer, leading to undesired oxidation. To fully restore the corrosion resistance of stainless steel and prevent any interference in the passivation process, it is imperative to remove heat tint and other surface contaminants.
SURFOX: A Comprehensive Cleaning Solution
SURFOX emerges as a safe, efficient, and swift electrochemical cleaning system. The system's welding cleaning rate ranges between 3-5 feet per minute. By harnessing the cleaning power of electrical current and the passivation properties of electrolyte cleaning solutions, the SURFOX system ensures a comprehensive approach. Passivation begins immediately after the completion of the SURFOX electrochemical cleaning process, and it typically takes between 24 to 48 hours for passivation to be fully completed and stabilized.
Electrochemical Cleaning with SURFOX-G and SURFOX-T Solutions
Before engaging in the electrochemical cleaning process using SURFOX-G and SURFOX-T electrolyte solutions, it is essential to recognize its transformative impact. The "Before" state typically exhibits heat tint and various surface contaminants, while the "After" state showcases a surface that remains unaltered. Microscopic views of the stainless steel surface (x100) highlight the effectiveness of the AC Mode, where the surface is preserved without alterations.
AC Mode: Preserving Surface Integrity
The electrochemical cleaning process relies on the synergy of electrical current and the electrolyte cleaning solution, specifically SURFOX-G and SURFOX-T. This combination effectively removes heat tint without causing any damage or alteration to the surface of the parent material. The result is a pristine and residue-free surface that not only eliminates contaminants but also fosters the development of a uniform and stable chromium oxide passive layer. This layer acts as a robust shield, safeguarding the stainless steel surface from oxidation. It's crucial to note that electrochemical cleaning should be carried out in the AC (Alternating Current) mode, available on all SURFOX models.
DC Mode: Precision in Polishing
In the "Before" state, when the need for a polishing process arises, heat tint and surface contaminants are evident. Utilizing SURFOX-T electrolyte solution in the DC (Direct Current) mode enables electrochemical polishing. This process not only removes parent material from the workpiece but also enhances the brightness of the weld. Unlike the AC Mode, electrochemical polishing alters the surface, making it particularly suitable for cleaning welds on mirror-finished materials. Understanding the distinction between AC and DC modes ensures precision in choosing the right electrochemical process for the desired outcome.
SURFOX 305 Weld Cleaning System
The SURFOX 305, a patented electrochemical weld cleaning system designed for stainless steel and aluminum, stands out as the most powerful unit for a diverse range of jobs. It efficiently addresses the removal of heat tint from the heat-affected zone of MIG, TIG, and spot welds, ensuring a clean surface for the initiation of passivation on stainless steel without compromising the surface finish.
Effective Heat Tint Removal
The SURFOX 305 electrochemical weld cleaning system is a highly effective solution for eliminating heat tint in the heat-affected zone of welded stainless steel (TIG, Spot, and MIG). This process is achieved without altering the surface of the parent material. Moreover, it plays a pivotal role in promoting the formation of a uniform and durable chromium oxide passive layer, providing enhanced protection against further corrosion.
SURFOX serves as a safer, faster, and more cost-effective alternative to conventional methods such as hazardous pickling pastes, wire brushing, and grinding, which pose risks to both operators and the materials being worked on.
Advanced Features of SURFOX 305
The SURFOX 305, SKU: 54D315 is equipped with an integrated tank and flow-through system, ensuring precise delivery of the electrolyte solution directly to the workpiece. This design minimizes the potential for spillage or cross-contamination, enhancing operational safety and efficiency.
Additionally, the dynamic current control feature guarantees that the electrical current applied will not cause micropitting on the surface, preserving the integrity of the material being treated. With its powerful capabilities and advanced functionalities, the SURFOX 305 WALTER 54D315 weld cleaning system stands as a reliable and versatile solution for various welding applications.
- Switchable output: AC Mode: cleaning & marking - DC Mode: polishing & etching
- Easily cleans MIG welds, TIG & spot welds
- Exclusive quick-change brush system to easily change out accessories and reduce downtime
- Ability to clean larger and hard to reach areas with the new brushes
- Integrated reservoir reduces the potential for contaminating or spilling the electrolyte solution
- Built-in vapor dispersion system
SURFOX 205
The SURFOX 205, SKU: 54D215 industrial weld cleaning system, is meticulously crafted for everyday production use. Boasting extensive safety and productivity features, it minimizes consumable use while delivering economical cleaning and passivation of stainless steel TIG and spot welds. This durable production model is engineered to clean TIG and spot welds on stainless steel or MIG, TIG, and spot welds on aluminum. Additionally, with the use of separately sold special marking kits, it can mark surfaces of stainless steel, aluminum, and titanium.
Additional Features and Benefits
- Walter 54B009 Large Graphite Insert: 45 mm width, ideal for surface renewing or restoring, and cleaning the back of MIG welds.
- Built-in Fume Dispersion System: Requires a compressed air line for efficient fume dispersion.
- Switchable Output Modes:
- AC Mode: for cleaning and marking
- DC Mode: for polishing and etching
- Redesigned Pump and Tank: Maximized efficiency through thoughtful redesign.
- New Quick-Connect System: Enables quick assembly changes between 4 m and 9 m long wand assemblies (9m wand sold separately), enhancing versatility and convenience.
SURFOX TURBO
The SURFOX TURBO 54D045 is not just powerful and compact; it's also Walter's most lightweight and portable unit, making it the ideal choice for quick weld cleaning and repair jobs in the field. Specifically designed for efficiency, this unit excels in cleaning TIG, Spot, and light MIG welds on stainless steel, providing hassle-free and rapid weld cleaning and passivation.
Features: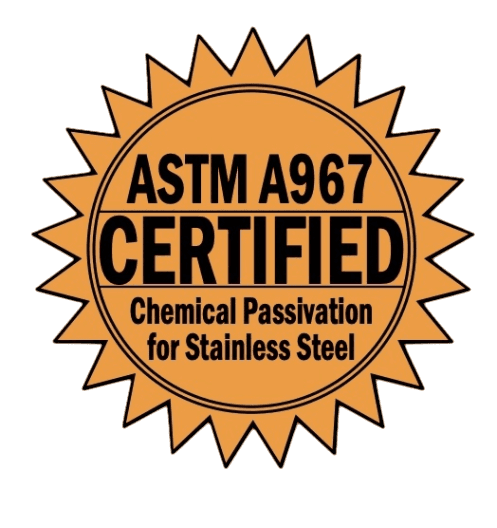
- Cleans Various Welds: Suitable for MIG, TIG, and Spot welds.
- Powerful and Compact: Despite its power, it remains lightweight and portable.
- Dip & Work Weld Cleaning: Streamlined process for user convenience.
- Simple to Use: Designed for easy operation.
- AC Only (Cleaning): Focused on efficient cleaning in AC mode.
Materials:
- Suitable for: Stainless steel
SURFOX TURBO ACCESSORIES
![]() |
![]() |
![]() |
![]() |
Walter Surface Technologies 54B038 SURFOX MINI Narrow Tungsten Insert | Walter Surface Technologies 54B028 SURFOX MINI Narrow Cleaning Pad with Plus Clamp Ring | Walter Surface Technologies 54B201 SURFOX TURBO Wand | Use with Model 54D045 |
Walter Surface Technologies 54B205 SURFOX TURBO Carbon Fiber Brush |
SURFOX MINI
Walter SURFOX Mini 53D055 is your ultimate companion for on-the-go maintenance. It is crafted for field and repair tasks due to it's compact design. The SURFOX Mini boasts an ergonomic design and a variable power setting, ensuring impeccable finishes even on the most delicate surfaces. What sets it apart is its innovative use of refillable electrolyte cartridges, eliminating the need for an integrated tank, reducing weight, and enhancing portability.
Perfect for repairs, touch-ups, and small-scale projects, this revamped unit excels in cleaning TIG or spot welds on stainless steel and MIG, TIG, or spot welds on aluminum. Additionally, it offers the versatility to mark stainless steel, aluminum, and titanium surfaces when paired with the SURFOX marking kit.
Additional Features and Benefits
- Cleans Various Welds: Suitable for MIG, TIG, and Spot welds
- Powerful and Compact: Despite its power, it remains lightweight and portable.
- Dip & Work Weld Cleaning: Streamlined process for user convenience.
- The SURFOX Mini comes equipped with a unique cartridge refilling pump. You can easily refill cartridges and save money by buying SURFOX electrolyte solutions in bulk packaging.